У радиолюбителя более 80% процентов творческого времени уходит на придание своей конструкции законченного вида, т.е. на «железо». Советов на этот счет много, но они у нашего Радиокота(как в общем-то и на других сайтах) разрознены и не систематизированы. Попробую восполнить этот пробел.
1.Корпус-это просто.
В некоторых случаях не требуется создания эксклюзивного внешнего вида. Это относится к различным измерительным приборам и прибамбасам к ним(фильтры, нагрузки и.т.п.). В этом случае корпус можно изготовить из двух П-образных панелей, одна из которых будет несущей конструкцией, а вторая декоративной крышкой. Наиболее доступный материал - оцинкованное железо. По поводу алюминиевых сплавов скажу следующее – мягкие хорошо гнутся, но сверленые отверстия в таком материале получаются нетоварного вида; твердые сплавы типа Д16-АТ замечательно пилятся и сверлятся, но плохо выдерживают изгиб на 90 градусов. Так что выбор за автором проекта.
Для изготовления гнутых панелей рекомендую сделать гибочное приспособление из стального уголка длиной 30-40см, показанное на рисунке, которое зажимается в тисках.
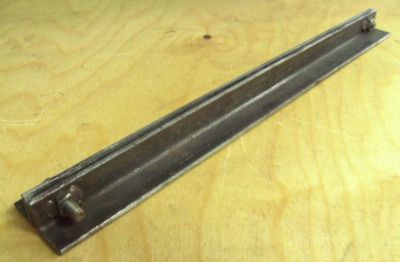
Рабочие поверхности уголков шлифуются наждачной бумагой. По краям просверлены отверстия под болты и приварены гайки М10 для дополнительного зажима длинных заготовок.
После разметки и вырезания заготовки, сверлятся и выпиливаются необходимые отверстия. Затем заготовка рихтуется (можно использовать поверхность тех же уголков) и выравниваются кромки. Маленькая хитрость – для выравнивания кромок лучше зажать в тисках большой плоский напильник без ручки, а по нему перемещать заготовку. Потом сгибаем заготовку по линиям разметки и оклеиваем наружные поверхности декоративной пленкой. В результате, после сборки, получается примерно вот такая конструкция.
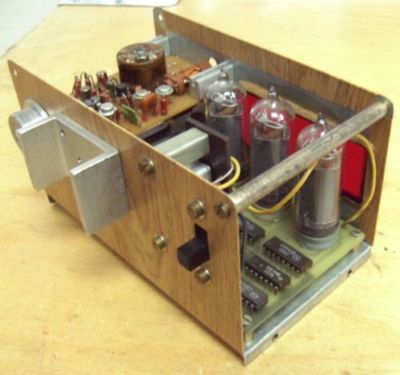
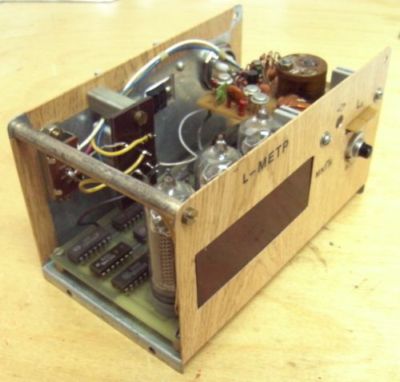
Для увеличения жесткости конструкции, в верхних углах передняя и задняя панели соединены с помощью дополнительных резьбовых стяжек. Использование декоративных винтов поможет облагородить внешний вид. Верхняя крышка изготавливается точно так же и крепится к несущей конструкции в нижней части с помощью винтов. Чтобы изделие не скользило по поверхности, снизу можно прикрепить резиновые втулки.
2. Угольник как таковой.
Если нет гибочного приспособления, для сборки конструкции можно воспользоваться универсальным угольником, предложенным В.Бесединым из г.Тюмень в журнале «Радио» №6 1993г. Стр.40. Заготовка вырезается из мягкой стали толщиной 2мм и показана на рисунке.
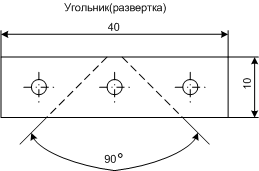
Изгибаем под прямым углом по штриховым линиям, сверлим отверстия, нарезаем резьбу М3 или М4 и получаем результат.
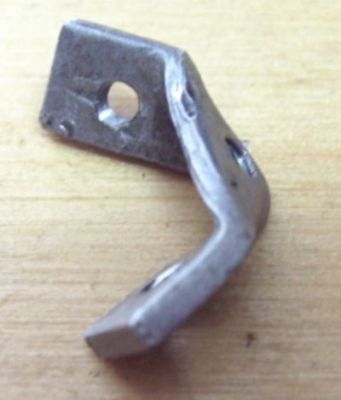
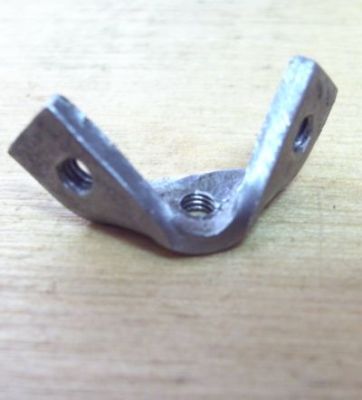
Полученный угольник монтируют в углу корпуса, там, где сходятся три смежные его панели. Размер заготовки варьируется исходя из своей конструкции. Если при разметке угол между линиями выбрать не равным 90 о, то прикрепляемая панель окажется наклоненной по отношению к противолежащей. Опыт конструирования приходит со временем. Поэтому начинающим стоит, для начала, склеить макет в натуральную величину из тонкого картона, посмотреть, как всё будет выглядеть на самом деле, и внести (если нужно) поправки.
3. Слово о заклепке.
В приснопамятные времена довелось на распродаже неликвидов одного оборонного предприятия приобрести потайные и полукруглые алюминиевые заклепки диаметром от 2 до 4мм. Они оказались как нельзя кстати при изготовлении различных шасси в домашних условиях. Технология несложная и требует лишь соблюдения нескольких условий:
1. Заклепка должна плотно входить в отверстия соединяемых деталей;
2. Соединяемые детали должны быть плотно сжаты;
3. Заклепка не должна выступать больше чем на 1,2 – 1,5 своего диаметра.
Расклепывать заклепку лучше с помощью обжимки, изготовленной из керна, у которого сошлифовано остриё и победитовым сверлом сделано углубление.

Расклепывание производят на ровной стальной поверхности. Для плотного сжатия соединяемых деталей (если заклепка туго входит в отверстия) их можно осадить с помощью стальной трубки диаметром чуть больше диаметра заклепки. При использовании заклепок с потайной головкой отверстие необходимо раззенковать. Это можно сделать сверлом с дополнительной насадкой, зенковкой или сверлом большого диаметра, заточенным под углом 90 градусов. Если заклепка слишком мало выступает из соединяемых деталей, можно раззенковать отверстие и со стороны клепки. Используя угольник, описанный ранее, можно получить примерно вот такую конструкцию.

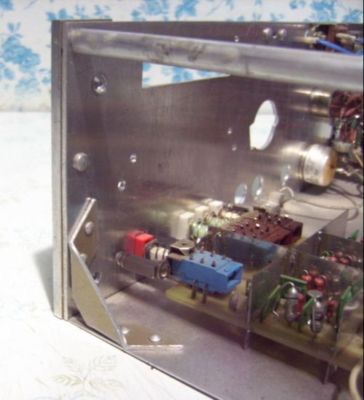
Если к несущей передней панели слева и справа приклепать полосы толщиной 4 – 5 мм, то между несущей и лицевой панелями появится пространство для винтов и гаек.
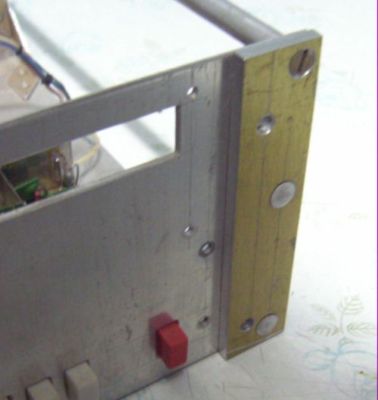
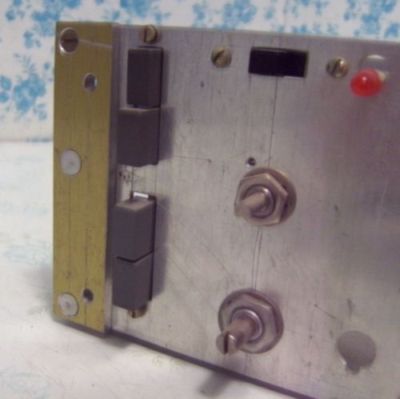
Такие же полосы, приклепанные снизу, позволяют закрепить шасси внутри какого – либо корпуса. Надо только предусмотреть в этих полосах резьбовые отверстия.
С помощью заклепок можно собирать комбинированные конструкции – например шасси из оцинкованного железа, а лицевая панель из листового алюминия.
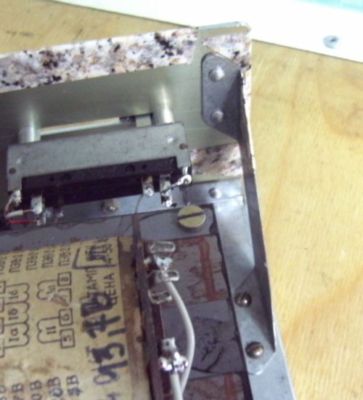
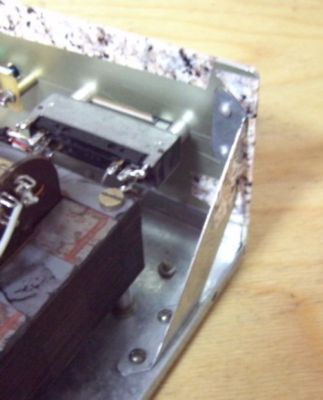
4. Втулки и стойки своими руками.
Непременным атрибутом любительской конструкции являются стойки и втулки различных размеров. Но, как правило, нужного размера не оказывается под рукой. Проблема легко решается, если есть электрическая дрель со струбциной для крепления к столу.
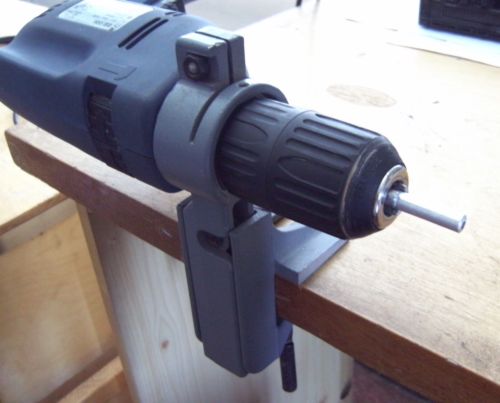
В качестве заготовок можно использовать старые длинные стойки, круглый ровный пруток и даже новые гвозди. Доводилось вытачивать мелкие втулки из латунных контактов старых электрических вилок. Для того чтобы наметить центр будущего отверстия, нужно изготовить универсальный кондуктор из стали, латуни или дюралюминия.
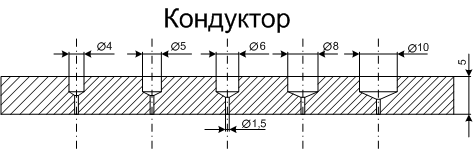
Зажав заготовку в патроне дрели, включаем её на 1/5 – 1/4 от максимальных оборотов. Плоским напильником шлифуем торец и снимаем фаску. Затем, через кондуктор, смазанный машинным маслом, сверлом 1,5мм, зажатым в патроне ручной дрели, намечаем центр. После этого, сверлом требуемого диаметра, проходим отверстие на глубину чуть больше длины будущей стойки, или, если стойка длинная, на глубину, достаточную для нарезания 5 – 6 ниток резьбы. Затем на штангенциркуле устанавливаем размер стойки с припуском 0,5мм для последующей обработки и отрезаем лобзиком с пилкой по металлу, как показано на следующем рисунке.
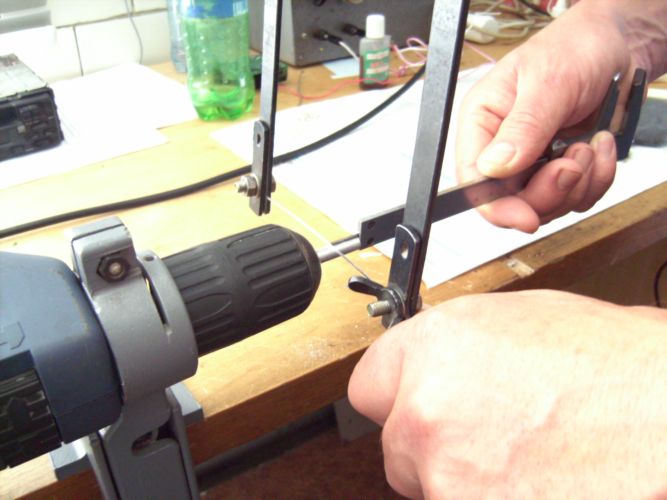
Втулка (стойка) почти готова. Осталось обработать второй торец и нарезать, если нужно, резьбу. При сверлении и нарезании резьбы необходимо смазывать сверло или метчик. Подойдет машинное масло, но лучший результат дает жидкость WD-40, знакомая каждому автолюбителю.
Замечу, что таким образом (с помощью лобзика) на осях можно делать проточки для разрезных запорных шайб.
В самом начале упоминались резьбовые стяжки. Но с ними всё просто в небольших конструкциях. При увеличении размеров возникает проблема с изготовлением такой стяжки большой длины. Выход есть – использовать две резьбовые втулки и шпильку нужной длины между ними. Шпилька изготавливается из любого ровного прутка (у автора под рукой чаще всего оказывались сварочные электроды).
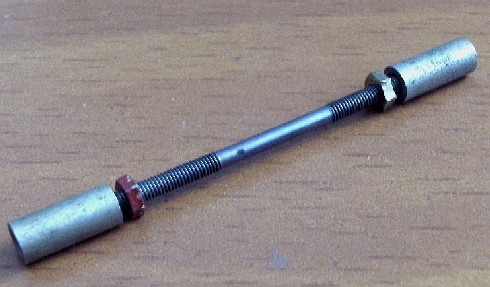
5. Радиатор на любой вкус.
При изготовлении конструкции желательно, чтобы задняя панель выполняла роль радиатора. Но где его взять по размеру своего устройства? Есть несколько вариантов:
1.Задняя панель изготовлена из алюминия толщиной 2-3мм. В этом случае, в месте установки транзисторов или микросхем, снаружи привинчиваются несколько небольших радиаторов, смазанных теплопроводящей пастой. Это могут быть радиаторы заводского изготовления, отрезки П-образного алюминиевого профиля и даже отрезки профиля от карнизов для штор. Если панель окрашена или оклеена, то участок под радиаторы зачищается до металла панели. Конечно, тепловое сопротивление такого радиатора увеличится по сравнению с цельнолитым, но обеспечит нормальный отвод тепла, а конструкция будет греть душу мастера.
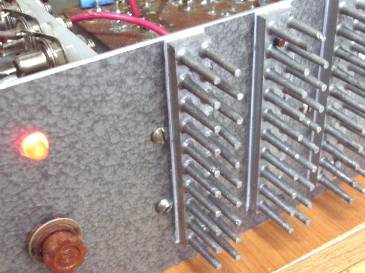
2.Задняя панель изготовлена из тонкого металла. В этом случае в задней панели вырезается окно. Радиатор крепится снаружи, а непосредственно к нему изнутри привинчивается транзистор или микросхема.


3.Можно также использовать один или несколько радиаторов в качестве элементов составной задней панели..

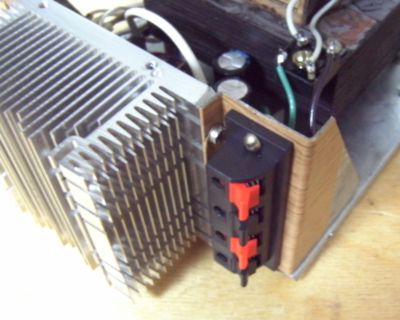